Traditionally, Total Cost of Ownership (TCO) has been a calculation intended to help buyers and owners determine the direct and indirect costs of procuring a product. In supply chain management, vendor managed inventory programs involve managing the process up to and including point of use on an assembly line. In this case, the calculation includes the direct and indirect cost of procuring a product but extends beyond the procurement process to include the costs incurred throughout the supply chain to assure a smooth integration into a final assembly.
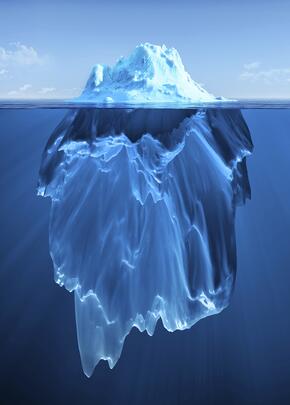
The materiality and value of each component of the TCO in Supply Chain Management will vary significantly by item depending on specific characteristics, some of which include:
- Item value
- Minimum order quantities
- Material content
- Physical characteristics
- Method of delivery/lead time/freight and logistics
- Source of supply
- Volatility of demand
- Product life cycle/obsolescence
- Order processing costs
- Application
- Program management costs
- Opportunity costs
Item value, minimum order requirements, material content, physical characteristics, method of delivery and lead time, source of supply, volatility of demand, and product life cycle all influence ordering and stocking decisions in a properly managed supply chain. Understanding these components and their respective impact on investment requirements and investment risk is critical to understanding the TCO. These components impact the inventory processing and holding costs such as warehousing labor, occupancy, and financing costs. For example, high value items result in higher financing costs while smaller, lightweight items (physical characteristics) can require little or no additional facilities or labor to handle.
These components also can impact investment risk, an often under estimated component of TCO. Lead time, volatility of demand, and product life cycle all impact investment risk in the form of dormant or obsolete inventory. Dormant inventory is inventory with no activity for long periods of time and obsolete inventory is inventory that has reached the end of its product life cycle. Detailed analytics are essential to optimize inventory with consideration for these components.
Order processing costs may seem like an obvious component of TCO, but the materiality of its impact on TCO can vary significant based on the previously mentioned components and even more significantly from one organization or industry to another. For example, a capital equipment manufacturer may not have the same systems and efficiencies in its order processing methodologies as an electronic assembly house with systems designed to handle a higher number of components and purchasing transactions. Supply chain management systems drive order processing methodologies focused on timely and efficient communication with suppliers optimizing order processing costs eliminating the burden on manufacturers. The duration of order processing should be included in the lead time of a good and is directly correlated to the order processing cost. Optimized systems with the right part profiles complete order processes instantaneously.
The application for an item directly influences the total cost of ownership. Understanding the application defines engineering, quality, and technical requirements. The best in supply chain management companies engage in understanding applications to add expertise specific to product classes outsourced. For example, products utilized in high temperature or corrosive environments may require certification of suppliers and materials combined with specialized plating all with little or no tolerance of variance in the manufacturing processes.
Vendor managed inventory costs are the single biggest variable in understanding the total cost of ownership in supply chain management once getting by the product characteristics. Developing tailored programs that match customer requirements and expectations requires attention to detail as does understanding the cost of those services. Some customers may be facing capacity issues limiting available space resulting in offsite storage and variations in the type of program needed to facilitate the smoothest flow of goods to assembly lines. Others may have excess capacity and desire higher volumes of onsite inventory requiring lower replenishment costs. Supply chain experts analyze your processes and develop a program to optimize the total cost of ownership for your situation.
Opportunity cost is the most overlooked component of the total cost of ownership. Where do you generate the most value? What is the lost opportunity if you are taking time away from your core competencies? The additional work and attention to detail to accurately measure and optimize the total cost of ownership takes focus and a partner who recognizes the process as part of their competency so you can focus on yours.
The calculation for Total cost of ownership (TCO) has been around for decades in its simplest form. For supply chain management companies, the equation has been extended along with integration in customers processes, improved analytics, and the desire to be the best in our core competencies.